
I/F conversion circuit is a current/frequency conversion circuit that converts analog current into pulse frequency.
In terms of navigation and motion tracking, AHRS (Attitude and Heading Reference System) and IMU (Inertial Measurement Unit) are two key technologies that play a vital role. Both AHRS and IMU are designed to provide accurate data about an object's orientation and motion, but they differ in components, functionality, and reliance on external reference fields.
AHRS, as the name suggests, is a reference system used to determine the attitude and heading of an object. It consists of an accelerometer, magnetometer, and gyroscope, which work together to provide a comprehensive understanding of an object's orientation in space. AHRS's true reference comes from the Earth's gravity and magnetic field, which allows it to accurately determine the position and orientation of objects relative to Earth's reference frame.
An IMU, on the other hand, is an inertial measurement unit capable of decomposing all motion into linear and rotational components. It consists of an accelerometer that measures linear motion and a gyroscope that measures rotational motion. Unlike AHRS, IMU does not rely on external reference fields such as Earth's gravity and magnetic field to determine orientation, making its operation more independent.
One of the main differences between AHRS and IMUs is the number and types of sensors they contain. Compared to an IMU, an AHRS usually includes an additional magnetic field sensor. This is due to the architectural differences in the sensor devices used in AHRS and IMU. AHRS typically uses low-cost MEMS (microelectromechanical systems) sensors, which, while cost-effective, may exhibit high noise levels in their measurements. Over time, this can lead to inaccuracies in determining object poses, requiring corrections to be made by relying on external reference fields.
In contrast, IMUs are equipped with relatively complex sensors, such as fiber optic gyroscopes or mechanical gyroscopes, which have higher precision and accuracy compared to MEMS gyroscopes. Although these high-precision gyroscopes cost significantly more, they provide more reliable and stable measurements, reducing the need for corrections to external reference fields.
From a marketing perspective, it's important to understand what these differences mean. AHRS relies on an external reference field and is a cost-effective solution for applications where high accuracy is not important. Its ability to provide accurate directional data despite the support of external fields makes it suitable for a range of commercial and industrial applications.
IMUs, on the other hand, emphasize precision and accuracy, making them ideal for applications where reliable and stable measurements are critical, such as aerospace, defense, and high-precision navigation systems. While IMUs may cost more, their superior performance and reduced reliance on external reference fields make them an attractive option for industries where accuracy cannot be compromised.
In summary, AHRS and IMU are indispensable tools for measuring direction and motion, and each tool has its own advantages and considerations. Understanding the differences between these technologies is critical to making informed decisions when selecting the most appropriate solution for a specific application. Whether it is the cost-effective reliance on external reference fields in AHRS or the high precision and accuracy of IMUs, both technologies offer unique value propositions that address different industry needs.
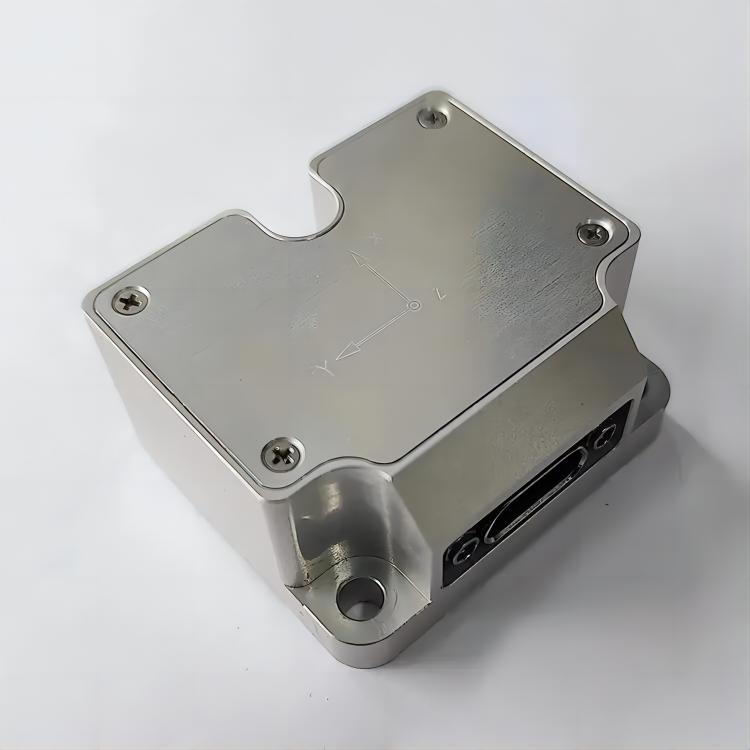
Post time: Jul-09-2024